Maersk is a Danish conglomerate and an integrated container logistics company. With a presence in over 130 countries, it is recognized as the world's largest container ship and supply vessel operator. Founded over a century ago in 1904, Maersk has evolved into a global leader. The company is renowned for its dedication to sustainability and has set bold targets to reduce carbon emissions and promote social responsibility across its operations.
Problem Statement
At Frankfurt airport, Maersk works with two warehouses to handle the temporary storage of cargo. Communication with these warehouses was happening via email and phone, and by inputting shipments into the separate systems of the warehouses. With dozens of shipments arriving and departing on a daily basis, this means a lot of manual communication - and lots of possible errors and delays. On top of that, you’re missing out on the scalability and flexibility that technologies like EDI (Electronic Data Interchange) offer to automate these processes. It makes perfect sense for Maersk to look towards data integration opportunities. However, developing a solution in-house would take months and bring friction to daily operations.
Enter, Mileviewer!
Mileviewer allows us to provide better customer service while simplifying our daily operations at the same time.
Solution
We kicked off with our Mileviewer Quick Scan, where we mapped out the integration opportunities between Maersk Frankfurt and their two warehouses. In a matter of days, we gathered and mapped all requirements concerning data and system integration:
- What data needs to be sent, and in which format
- At what moment or by which triggers
- Using which technologies
As a result of this Quick Scan, we are then able to rapidly build the connectors which will integrate the systems.
First, for cargo departing from Frankfurt, we need to connect to the export warehouse so when a new shipment is booked, all details are immediately available in their system.
Secondly, for cargo arriving in Frankfurt, whenever the Maersk Frankfurt office accepts a shipment, it should automatically be sent to both the import warehouse and the cargo handler. All of this communication would now happen automatically thanks to our implementation.
And finally, all shipment details were to be continuously synchronized between Mileviewer and Maerks's TMS system.During the development and integration phase, we worked closely with Maersk’s IT team, as well as with the warehouse teams.
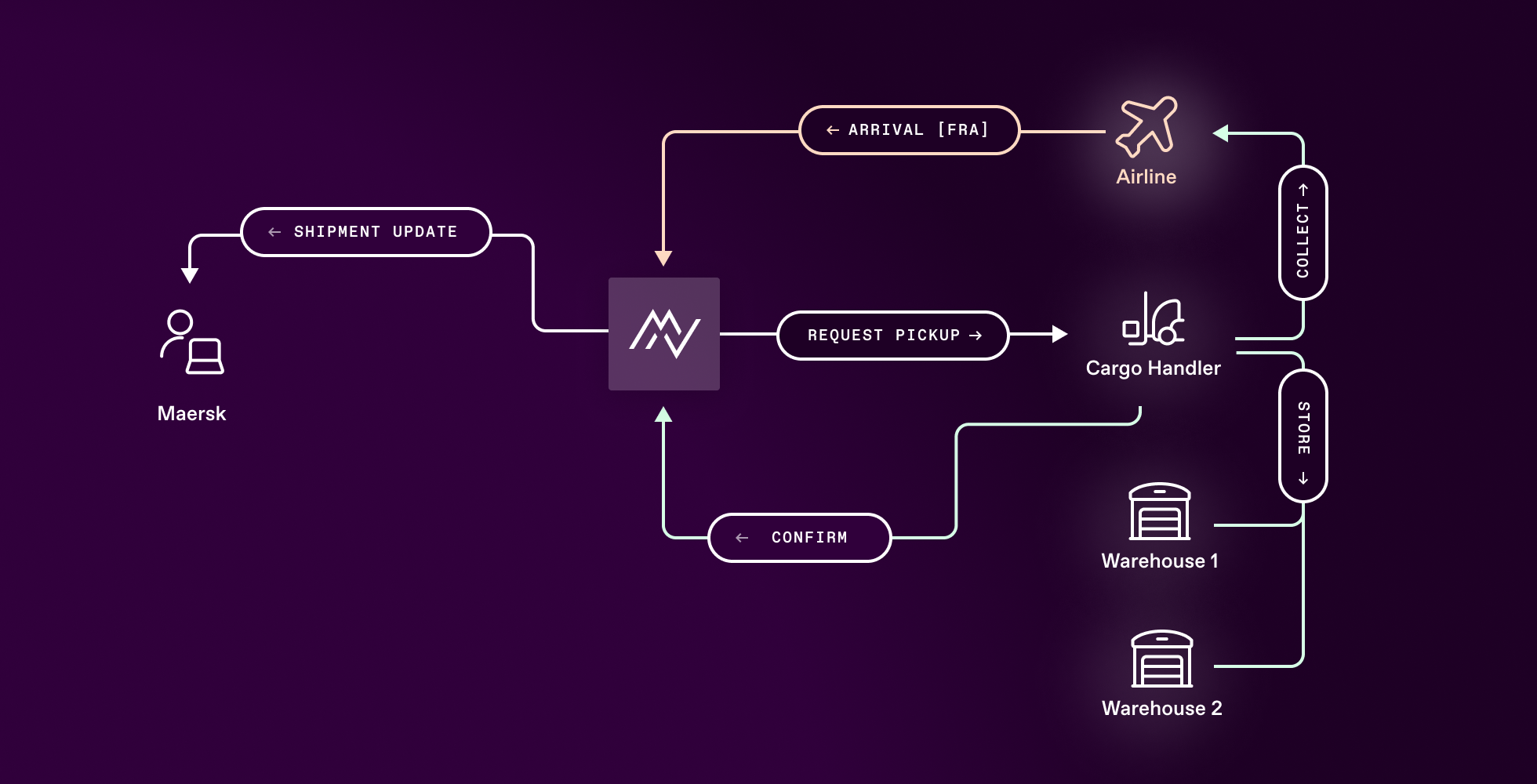
A Maersk key user with extensive system and process knowledge was involved throughout the whole project to test and provide feedback.When the time came to put the new solution to the test, we organized a two-week shadow run to make sure everything would run at speed, scale and accuracy. This approach allows us to tackle any remaining edge cases quickly, so we can have the most reliable production setup possible.
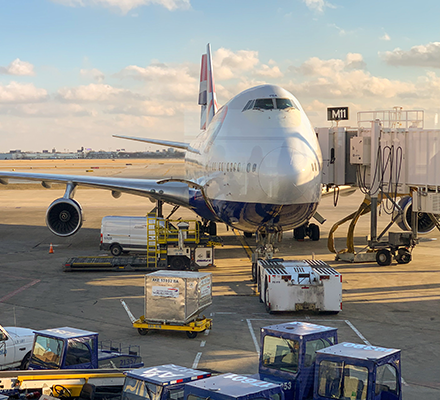
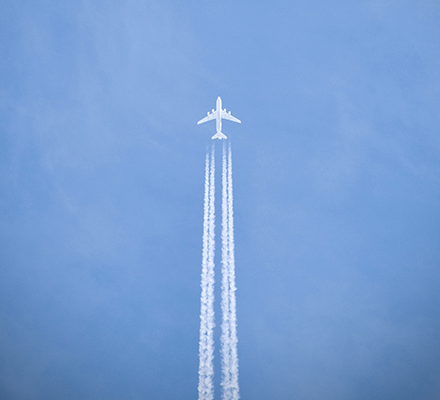
Conclusion
Leveraging technologies like EDI and API can support more effective collaboration and communication between logistics partners. This will not only help to build stronger relationships and improve overall efficiency, it's a key factor to staying ahead in today's market. For Maersk, a project like this allows them to adapt and innovate at high speed, without impacting daily operations or customer satisfaction. These high speeds can be achieved thanks to our extensive knowledge in both logistics and technology.
Used in 47 Maersk offices worldwide
Improved visibility and accuracy of shipment details
Major increases in cost and time efficiency