TOMRA Food is a leading provider of food sorting and grading solutions, using cutting-edge technology to help food processors optimize their operations and maximize their yield. With over 8,000 installations in more than 80 countries, TOMRA Food faces several logistics challenges related to the transportation, installation, and maintenance of their equipment.
Problem Statement
For their clients, TOMRA Food operates within certain service level agreements. Next to general maintenance and regular service for optimal performance, this includes delivering on-site repairs and shipping spare parts. When support is needed for a specific client, TOMRA Food needs to manage to get both a technician and the required parts to the site, on time. Failing to do so results in unsatisfied customers and potential penalty fees. But this can be a real challenge on a global scale with different logistics service providers and technical partners. So to cut costs and raise their service levels to new heights, TOMRA Food was looking for a better way to manage spare parts shipment and work order planning.
"Mileviewer allows us to clearly see shipment statuses in a way that's relevant for us."
Solution
An ERP system (IFS) was already in place, but it didn’t allow for an integrated way of managing shipments with different service providers. So from the start, TOMRA Food worked with our business analysis team to accurately map both internal and external tools, processes, and data. When this audit was done, there was a clear overview in terms of:
- Key users
- Business requirements
- Data mapping
- Integration needs
We went on to translate this into an agile project approach that would allow swift delivery of the different milestones. As the pilot project for TOMRA Food Global, it was also important to define the foundation on which other sites would build. In a matter of weeks, data communication was streamlined and integrated into the ERP system. We leveraged both off-the-shelf integrations that are in Mileviewer’s library with custom development efforts to integrate existing systems. Users no longer had to send dozens of e-mails and consult multiple 3PL websites to efficiently ship and plan maintenance and support.
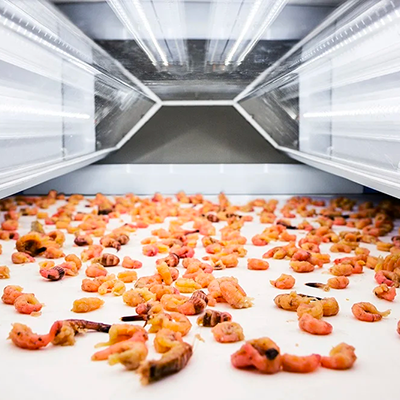
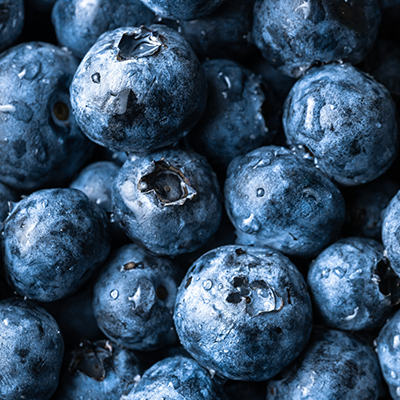
Conclusion
Mileviewer enables TOMRA Food to view shipments on parcel level or per plant. So no more need to send e-mails back and forth to find out where a spare part is. And in turn, work orders for technicians can be planned more precisely. There’s also a significant decrease in time spent managing shipments, allowing for more cost-efficient management of the team. But more importantly, Mileviewer makes it unnecessary to develop extensive (and slow) bespoke integrations with all the external agents. By rolling out our solution, TOMRA Food now has an extra way of ensuring data quality. Mileviewer, by acting as a universal adapter between the ERP system and the logistics service providers, can identify data entry errors and bring them to awareness. Spending time looking for missing or incorrect tracking IDs is a thing of the past.
Improved shipment visibility
Less time spent managing shipments
Increased data quality